Quality & Production Courses
"Quality is not an act, it is a habit. – Aristotle
Investing in quality training today builds the habits and skills that ensure excellence, reliability, and success in everything you do tomorrow."
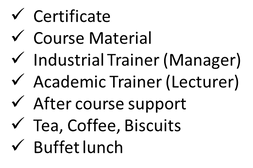

Quality Control (QC) and Quality Assurance (QA)
A Quality Control (QC) and Quality Assurance (QA) course is generally suited for professionals working or intending to work in roles related to quality management, product development, production, or service delivery. It is beneficial for individuals who are looking to:
Pursue careers in quality management in manufacturing, pharmaceuticals, software development, or any other industry that requires strict quality standards.
Improve their understanding of industry-specific quality standards and protocols.
Transition into roles like quality manager, process improvement specialist, or QC/QA specialist.
Learn how to ensure products and services meet the required standards and satisfy customer expectations.
Benefits of a QC/QA Course:
Career Advancement: Completing a QC/QA course can enhance career prospects, providing individuals with the skills and knowledge needed to enter or advance in quality management roles.
Increased Employability: Organizations are always looking for professionals with a solid understanding of quality control and assurance practices to ensure the production of defect-free products.
Enhanced Skill Set: Gain specialized knowledge in methodologies like Six Sigma, Lean, and Total Quality Management (TQM).
Cost Reduction for Organizations: By identifying and addressing issues early in the development or production process, QC/QA professionals help companies avoid costly mistakes and rework.
Improved Product or Service Quality: The focus of QC and QA is on improving and maintaining consistent quality, leading to customer satisfaction and loyalty.
Topics Typically Covered:
Introduction to Quality Management:
Definition of quality and its importance.
The role of QC and QA in business.
Types of quality standards and frameworks (ISO, FDA, etc.).
Quality Control (QC):
The concept and techniques of inspection and testing.
Statistical process control (SPC) tools and techniques.
Visual inspections and product sampling.
Testing equipment, calibration, and maintenance.
Defect tracking and root cause analysis.
Quality Assurance (QA):
Difference between QA and QC.
Process management and improvement methodologies.
Documentation and reporting in quality assurance.
Auditing and compliance (internal and external audits).
Risk management and quality planning.
Methodologies and Tools:
Six Sigma: A data-driven approach to improve processes by eliminating defects.
Lean: A methodology to streamline processes by eliminating waste and improving flow.
Total Quality Management (TQM): A holistic approach to continuous improvement in all areas of a business.
Failure Mode and Effect Analysis (FMEA): A structured approach to identifying potential failure points in a process.
Root Cause Analysis: Techniques to identify the root causes of problems rather than just addressing the symptoms.
Statistical Tools in QC and QA:
Control charts, histograms, Pareto charts.
Regression analysis and hypothesis testing.
Standards and Regulatory Compliance:
ISO 9001, ISO 14001, and other standards.
Understanding of industry regulations (such as FDA, GMP).
Auditing procedures and compliance checks.
Quality Improvement Projects:
Practical application of quality principles to real-world problems.
Case studies and problem-solving exercises.
Relevant Industries:
Manufacturing: Ensuring product quality through testing, inspections, and compliance with standards like ISO 9001.
Pharmaceuticals and Healthcare: Regulatory compliance, quality assurance of drugs and medical devices (e.g., GMP, FDA regulations).
Software and IT: QA practices in software development, including software testing, continuous integration, and Agile methodologies.
Automotive: Implementing quality controls in vehicle production, focusing on safety and reliability.
Food and Beverage: Ensuring product safety and quality standards compliance.
Aerospace: Meeting high industry standards in product design, testing, and certification.
Energy and Utilities: Maintaining quality standards in equipment manufacturing and operational processes.
Consumer Electronics: Ensuring that products meet quality specifications and function as intended.