Quality & Production Courses
"Quality is not an act, it is a habit. – Aristotle
Investing in quality training today builds the habits and skills that ensure excellence, reliability, and success in everything you do tomorrow."
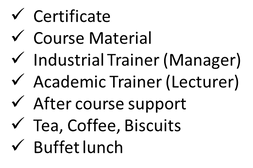

Process Mapping and Improvement
A Process Mapping and Improvement course is designed to teach professionals how to identify, analyze, and improve organizational processes to enhance efficiency, reduce waste, and optimize performance. These skills are valuable for anyone involved in business process management, operations, or quality improvement.
Who Is It For?
This course is suitable for:
Business Analysts: They can use process mapping to understand and improve workflows.
Operations Managers: Process improvement is key for streamlining operations.
Quality Assurance Professionals: Process improvement is integral to ensuring high-quality outcomes.
Project Managers: They need to map and improve processes for project execution.
Consultants: Those helping organizations identify inefficiencies and improve performance.
Supply Chain and Logistics Professionals: They can use process mapping to optimize distribution and inventory management.
Anyone in a role focused on operational efficiency, continuous improvement, or cost reduction.
Benefits of the Course
Improved Process Efficiency: Learn how to identify bottlenecks and inefficiencies, making processes smoother and faster.
Enhanced Problem-Solving Skills: Participants gain a structured approach to solving issues in operations.
Cost Savings: Process improvements typically lead to reduced costs through the elimination of waste or inefficiencies.
Better Decision Making: With clear process mapping, decision-makers can base their strategies on a visual representation of how things work.
Cross-Functional Collaboration: Helps in aligning teams from various departments by providing a shared visual understanding of processes.
Boosted Customer Satisfaction: More efficient processes often result in quicker response times, improved service quality, and better product delivery.
Professional Development: The course builds competencies in process management, improving career prospects in multiple industries.
Topics Covered
Introduction to Process Mapping
Basic concepts of process mapping
The importance of process mapping in business
Different types of process maps (e.g., flowcharts, SIPOC diagrams, value stream mapping)
Tools and Techniques
How to use common process mapping tools like Microsoft Visio, Lucidchart, or Bizagi
Symbols used in process mapping (e.g., ovals, rectangles, diamonds)
Understanding Processes and Workflows
Identifying key inputs, outputs, and stakeholders
Mapping current (as-is) processes
Mapping future (to-be) processes
Process Analysis
Identifying inefficiencies, bottlenecks, and waste
Tools for process analysis, such as Fishbone Diagrams and Pareto Analysis
Process Improvement Strategies
Lean Six Sigma principles
Continuous Improvement methods like Kaizen
Root Cause Analysis
Redesigning processes for better performance
Metrics and Key Performance Indicators (KPIs)
Identifying and tracking KPIs for process success
Measuring performance before and after improvements
Change Management
Handling resistance to change
Communicating process changes effectively
Ensuring sustainability of improvements
Case Studies and Real-Life Applications
Industry-specific case studies to demonstrate process mapping and improvement
Hands-on practice with sample processes
Advanced Topics (Optional)
Automation of processes using RPA (Robotic Process Automation)
Integration of process mapping with ERP systems
Relevant Industries
Process mapping and improvement are applicable in a wide variety of industries, including:
Manufacturing: Improving production processes, reducing downtime, and optimizing supply chains.
Healthcare: Streamlining patient care processes, reducing wait times, and ensuring compliance with health regulations.
Finance and Banking: Improving transaction processes, fraud detection, and customer service operations.
Information Technology: Optimizing software development cycles, IT service management, and system integration.
Logistics and Supply Chain: Streamlining transportation, warehousing, and inventory management.
Retail: Enhancing customer service, order fulfillment, and inventory management.
Government and Public Sector: Improving service delivery, reducing bureaucracy, and increasing transparency.
Consulting Firms: Advising organizations on process improvements.
Education: Improving administrative processes and student service workflows.
Energy and Utilities: Optimizing operational processes and reducing energy wastage.